Don't have an account?
Creating an account has many benefits: check out faster, keep more than one address, track orders and more.
Or
Checkout as a Guest
Place your order without creating an account for extra convenience.
When determining how often a thread gauge should be calibrated, the main two questions you should be asking are:
- How often is the piece of equipment used?
- What is the environment it is being used in?
If the thread gauge is being used on daily basis in a heavy production environment, it would be best practice to schedule calibration based on number of uses (for instance, 100 parts per use). Alternatively, if you process batches of parts consistently (for instance, 100 parts per month), you could calibrate at regular time intervals, say every two months.
Conversely, if the thread gauge is used solely in a well-maintained inspection room several times a week, once yearly calibration should be sufficient.
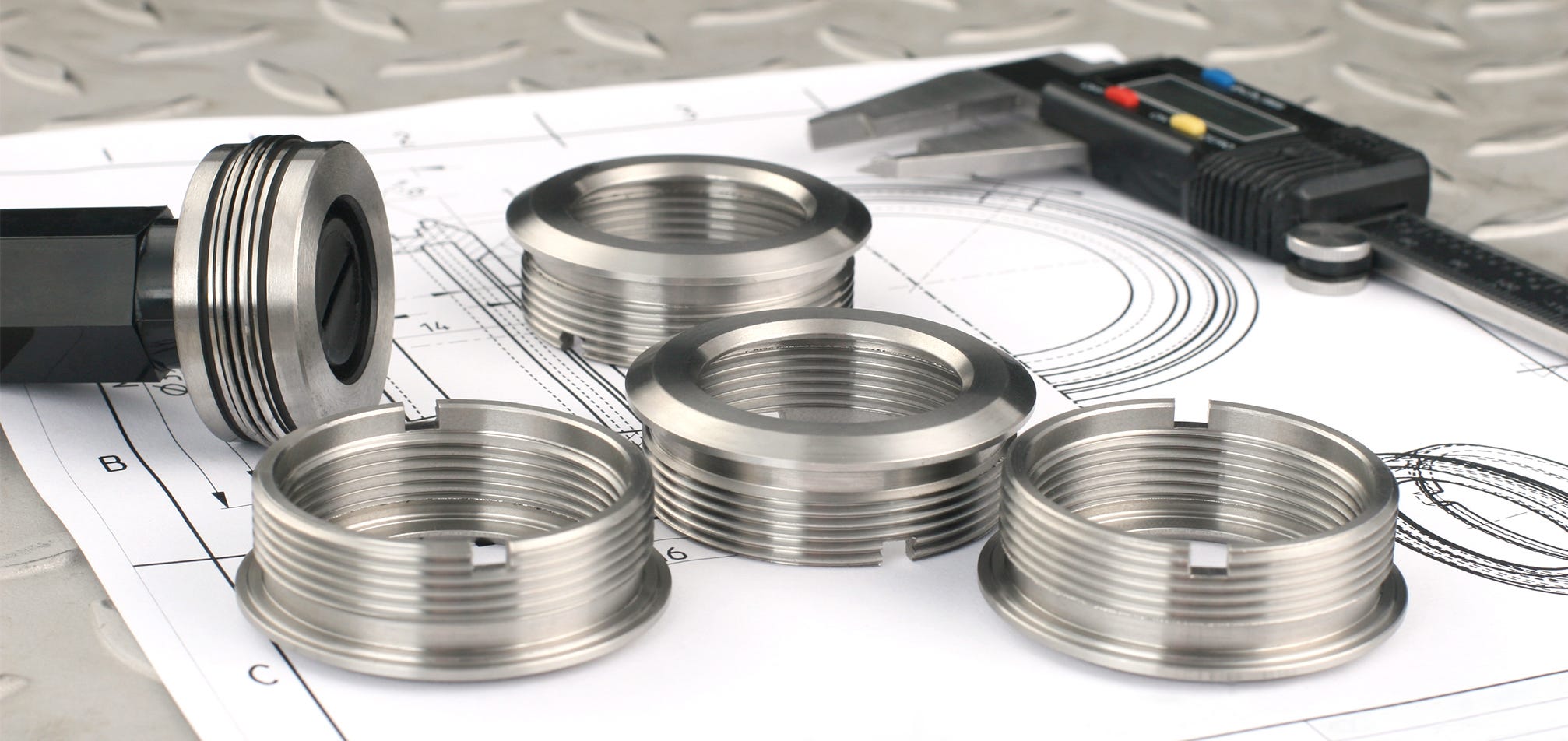
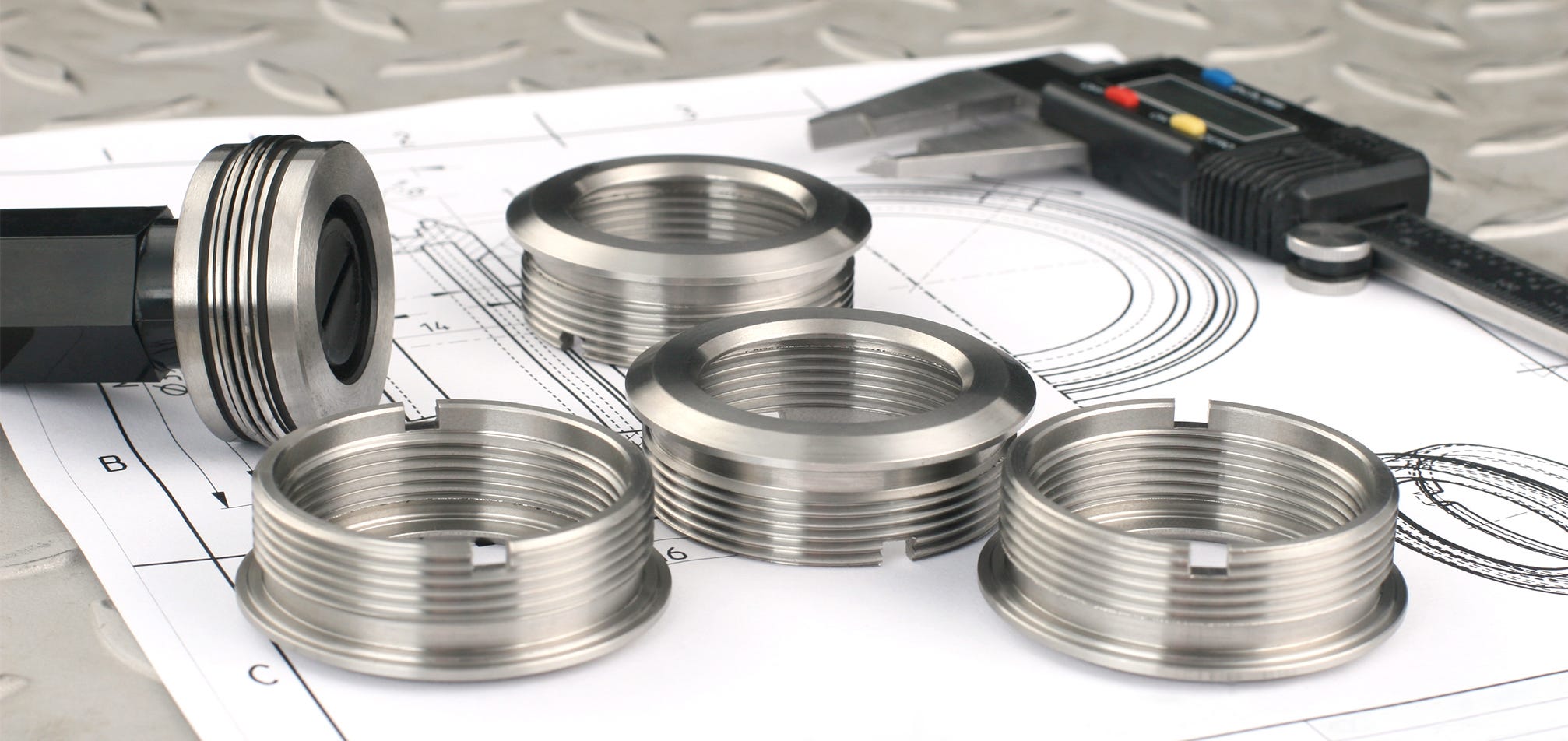
Other points worth noting which can determine calibration frequencies are:
- What material is the thread gauge coming into contact with? Is it soft or abrasive? If it is abrasive, the gauge will wear considerably more and so more frequent calibration is required.
- What are your customer requirements for thread gauge calibration? Some customers will require stricter tolerances and rigidity in your calibration regime than others.
From a cost and time perspective, utilising external calibration services is preferable unless you have an on-site inspection technician who has access to the required equipment. However, this would be my last resort due to the time the process can take and costs for external calibration are usually quite reasonable.
When using thread gauges for shop floor or inspection use, it is always recommended to keep proper documentation. Such documents should include information like:
- Gauge description.
- Serial number.
- Date of current/last inspection.
- Due date for next inspection.
- Location of gauge.
- Any additional notes.
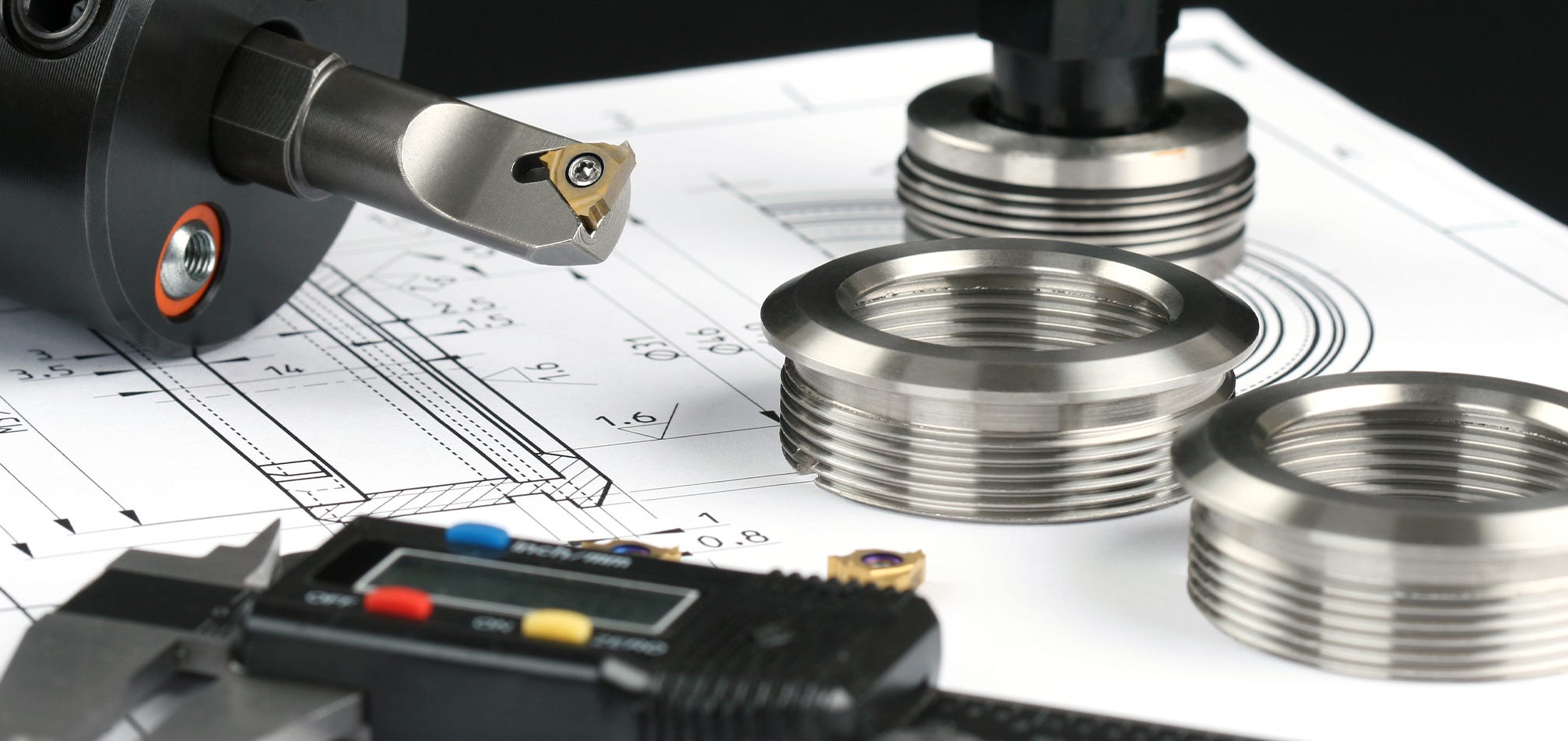
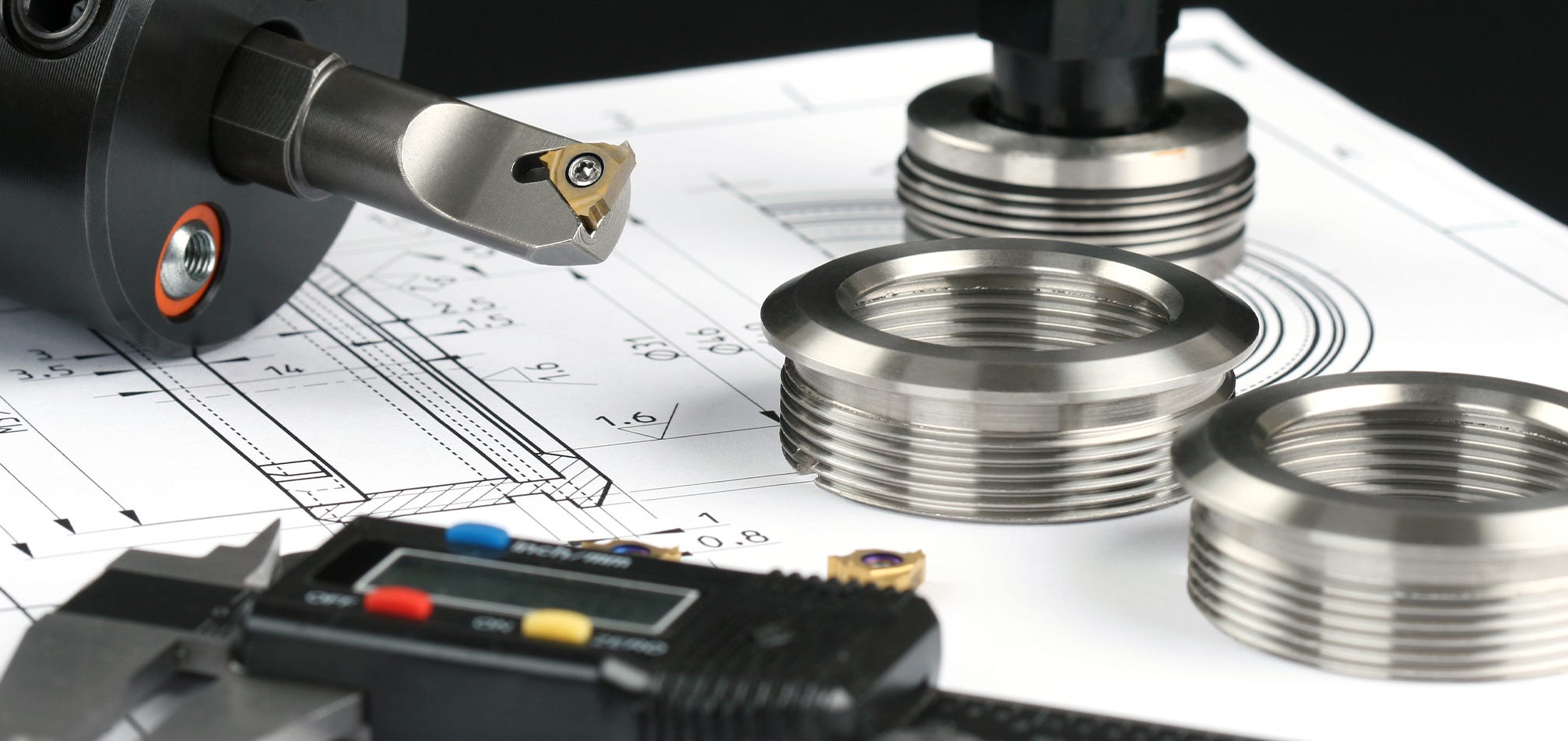
This is good for not only your own records but also for future audits. Each gauge will also need an identifying feature, be it a calibration sticker or colour coded blob of paint, to identify its status.
If the correct records are kept, schedules are followed and the gauges are used correctly, calibrating your gauges should not be hard work! The key question to ask yourself when planning a schedule is ‘how is that specific gauge being used?’
Finally, in my experience, I have found it very rare that a thread gauge will fail calibration unless the gauge has been dropped or damaged in some way.
Cutwel offer UKAS calibration on all of their thread ring and plug gauges, as well as a large portion of their measuring tools. For more information or if you have any further questions regarding calibration, call us today on 01924 869615, email sales@cutwel.net or browse our full thread gauge range at www.cutwel.co.uk.