Don't have an account?
Creating an account has many benefits: check out faster, keep more than one address, track orders and more.
Or
Checkout as a Guest
Place your order without creating an account for extra convenience.
Mastering Indexable Drills
Contents
- Introduction to Indexable Drills (U-Drills)
- Understand What U-Drills Are Best For
- Select the Right Insert Geometry & Grade
- Mind the Coolant Supply
- Optimize Feeds & Speeds
- Correct Entry and Exit
- Watch the Depth-to-Diameter Ratio
- Chip Control is Key
- On CNC Lathes: Use U-Drills as Boring Tools
- Secure Tool Holding & Setup
- Monitor Tool Wear
- Bonus: Common U-Drill Mistakes to Avoid
- Final Thoughts
Introduction to Indexable Drills (U-Drills)
Indexable drills, commonly known as U-drills, are powerful tools for high-performance drilling and rough boring operations. Whether you're working on a CNC lathe or a machining centre, these tools offer speed, repeatability, and cost-efficiency - but only when used correctly.
Here’s a comprehensive guide on best practices, tips, and tricks to get the most from your U-drills and avoid common pitfalls.
Understand What U-Drills Are Best For
U-drills use replaceable carbide inserts to drill holes rapidly and can also double as a rough boring tool. They're ideal for:
-
Drilling large holes (typically 12 mm and above)
-
Centreline and off-centre boring (in turning operations)
-
High-speed production environments
-
Soft steels to exotic alloys
Select the Right Insert Geometry & Grade
Inserts are not one-size-fits-all. Choose based on:
Material:
-
Steel: General-purpose or wear-resistant carbide with TiAlN coating
-
Stainless: Tougher grades with honed edges and sharp geometry
-
Aluminium: Uncoated or polished inserts with high rake
Application:
-
Center inserts typically handle more radial force
-
Periphery inserts manage higher cutting speeds
Tip: for best performance use the Korloy King Drill, it has excellent performance on all materials, for general or economic performance select the Mammut u-drill.
Mind the Coolant Supply
Coolant is critical for chip evacuation and tool life:
Optimize Feeds & Speeds
Don’t apply traditional drilling values. U-drills operate more like turning tools:
-
Speed: Based on the periphery insert (outer diameter)
-
Feed: Use manufacturer tables, but as a rule of thumb:
-
Steel: 0.08–0.2 mm/rev per insert
-
Stainless: 0.06–0.15 mm/rev
-
Aluminium: 0.1–0.25 mm/rev
-
Reduce feed when breaking into cavities or exiting angled surfaces
Tip: Start conservatively and dial in based on surface finish and chip formation.
Correct Entry and Exit
Avoid crashing or damaging inserts:
-
Ensure your starting surface is flat
-
If unavoidable, ramp in slowly or pre-spot with a flat-bottom drill
-
Avoid drilling through angled surfaces unless using a reduced feed and pilot
Watch the Depth-to-Diameter Ratio
Standard U-drills are most stable up to 3xD (depth = 3× diameter). For deeper holes:
-
Consider a pilot drill first
-
Use peck drilling cautiously - U-drills aren't ideal for it
-
Use a spade drill
Chip Control is Key
Poor chip evacuation is the #1 cause of tool failure with U-drills.
-
Ensure coolant pressure is adequate
-
Use correct chipbreaker geometry
-
Watch chips - long stringers or compressed “bird nests” are a red flag
Tip: If chips are wrapping or clogging, reduce feed or switch to a sharper geometry.
On CNC Lathes: Use U-Drills as Boring Tools
One huge advantage on lathes is their versatility:
-
Offset the U-drill on the X-axis and use it for rough boring
-
Great for ID profiling, saving a tool station
-
Use in combination with internal turning holders for finishing passes
Secure Tool Holding & Setup
-
Ensure U-drill is perfectly perpendicular to the workpiece
-
Use shortest possible overhang to reduce vibration
-
Check insert clamping torque - loose inserts = catastrophic failure
Monitor Tool Wear
Even though inserts are replaceable, poor wear monitoring leads to bad holes:
- Replace inserts as a pair (center and periphery)
- Use wear indicators or set tool life in your CNC program
- Pay attention to chatter, surface finish, and chip colour - they all reveal wear issues
Bonus: Common U-Drill Mistakes to Avoid
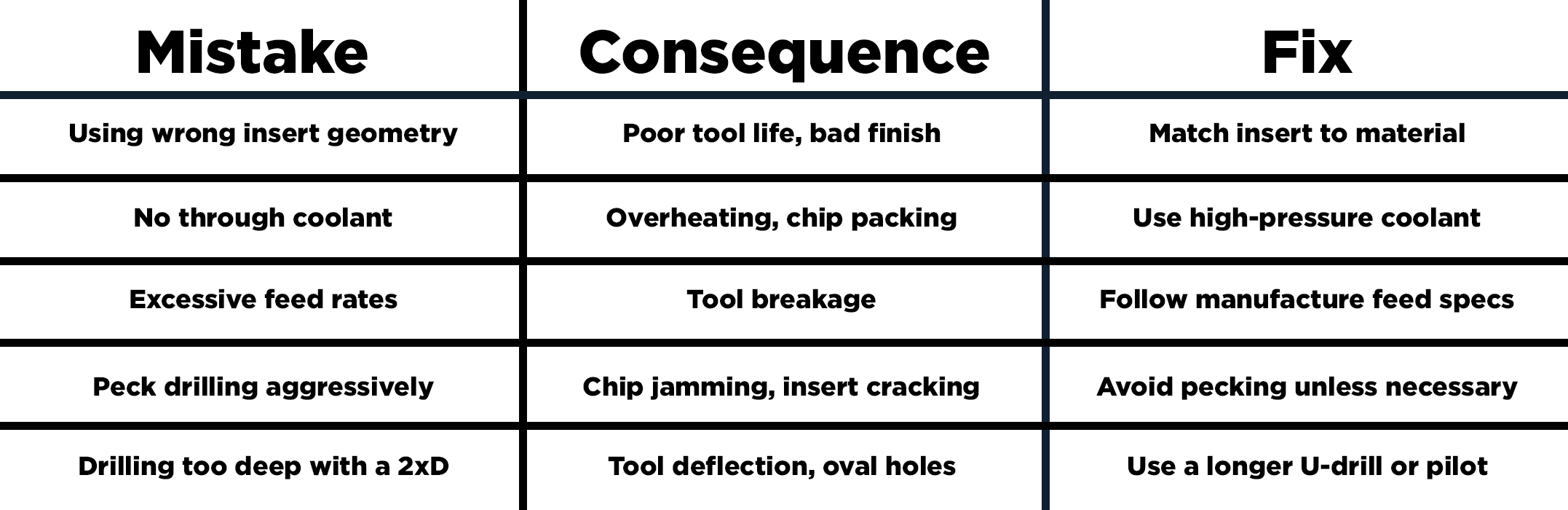
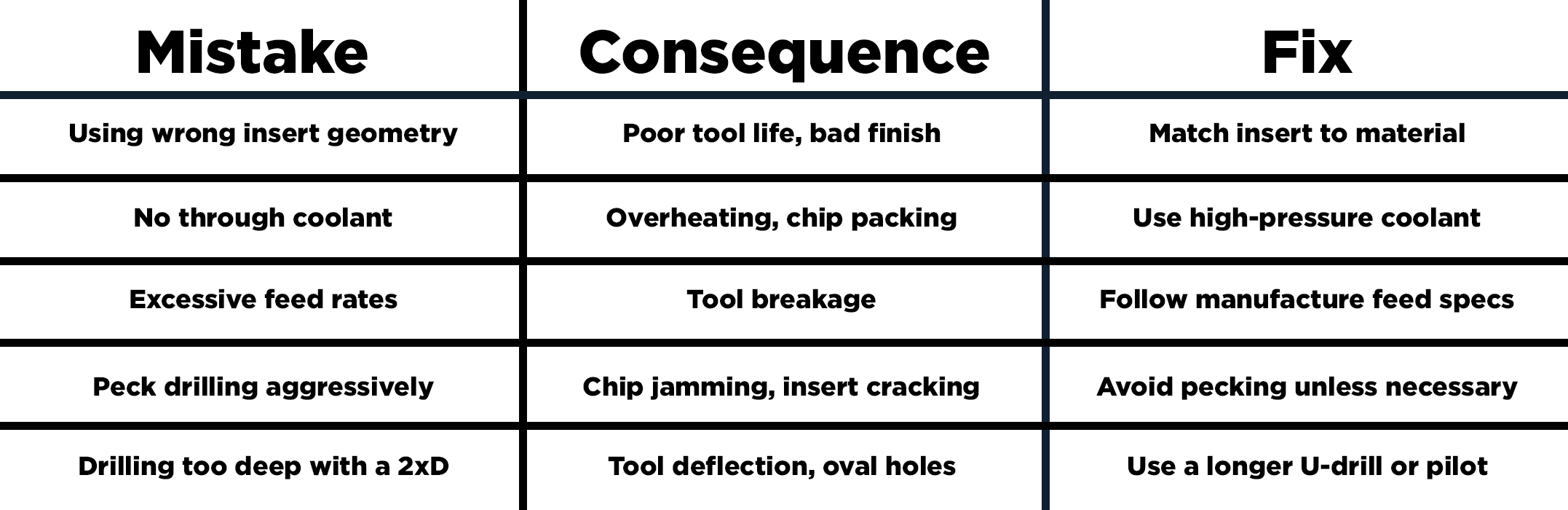
Final Thoughts
U-drills are production workhorses - when used correctly. By dialling in your feeds, maintaining coolant flow, choosing the right inserts, and following best practices for entry/exit, you can dramatically boost tool life, reduce cycle times, and improve hole quality.
Whether on a CNC lathe or a vertical machining centre, mastering U-drills gives you a serious edge in speed and productivity.
Got questions about vice alignment tools or setup accessories? Please contact our technical team on 01924 869 615 or email sales@cutwel.net.