Don't have an account?
Creating an account has many benefits: check out faster, keep more than one address, track orders and more.
Or
Checkout as a Guest
Place your order without creating an account for extra convenience.
In machining, what is chatter?
Chatter is known as the vibrations which can occur in a machine or on the workpiece. It can be either be fine or quite violent and generate a distinctive loud noise. Chatter can be detrimental to your tool life, surface finish and can also affect your component dimensionally, therefore it is best to eliminate any risk of chatter beforehand.
Chatter can feed on itself. A vibration in the tool leads to a wave in the work piece; constant vibration creates a steady series of these waves. Once the surface is chattered and your tool tries to take a 2nd pass over this surface, the tool will follow the waves and peaks and the chatter will intensify and become even worse!
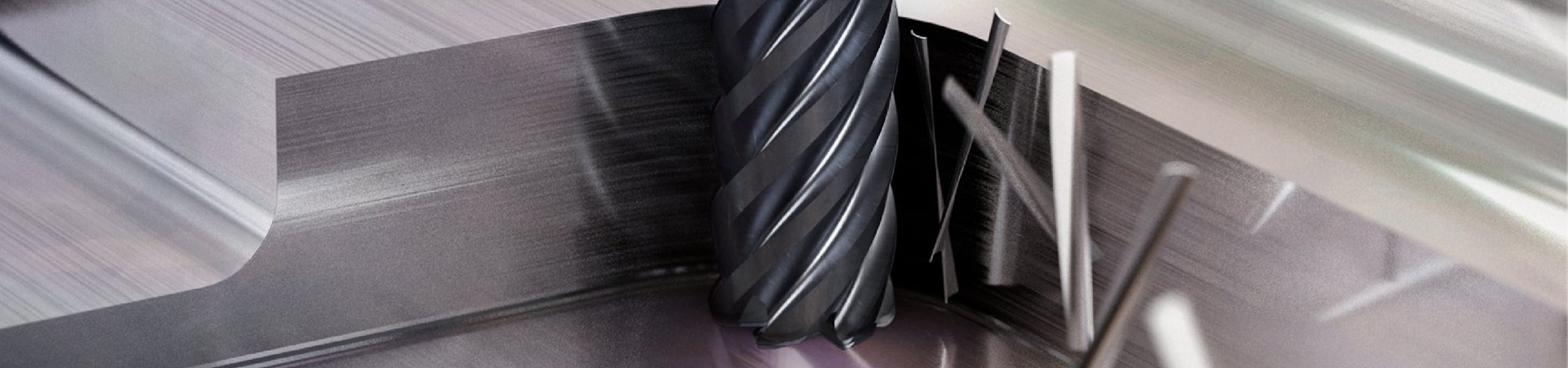
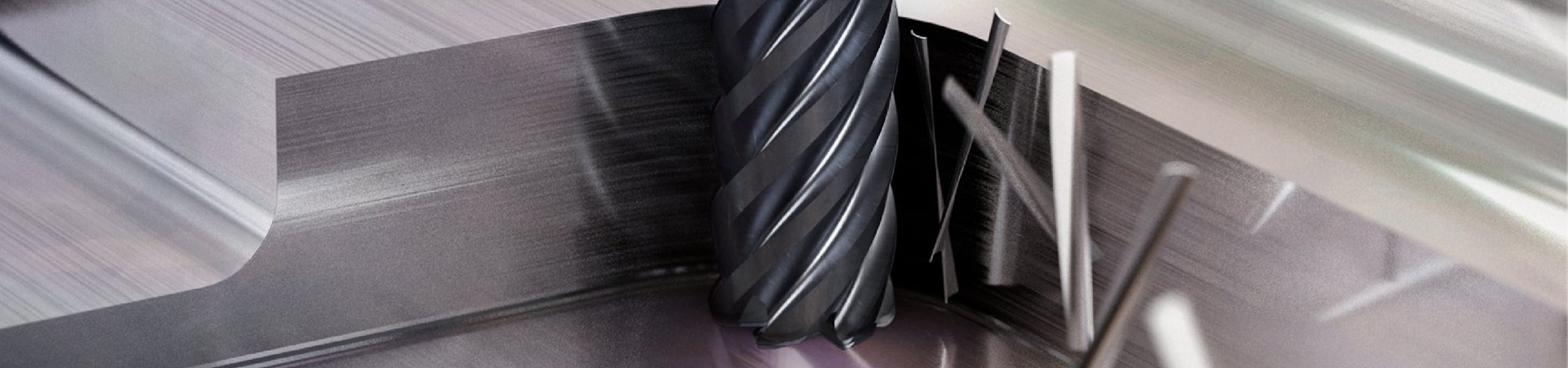
Types of chatter
There are two main types of chatter to be aware of:
TOOL CHATTER – Your machine and tool are doing the vibration which is transmitted to your workpiece. A couple of examples may be:
- The milling cutter sticking out of the tool holder too far (milling).
- Incorrect tool chosen for the job – boring bar diameter might be too small for the diameter of bore being cut (turning).
WORKPIECE CHATTER – Your Workpiece is doing the vibrating. For instance:
- The workpiece is sticking out of the vice or chuck too far.
- The workpiece has thin walls in places and has no support.
How to eliminate chatter when machining
Eliminating chatter comes down to 3 factors when setting up:


Workholding refers to the clamping method used to hold a workpiece in the machine ready for the machining process to take place.
- Maximise the grip and support on the work piece.
- Use correct chuck/jaws on a lathe and the correct vice on a milling machine.
- Make sure the workpiece is held and supported where the cutting force will be applied.
- Longer workpieces on a lathe may need the aid of a tailstock or a steady.


Tooling could be a milling cutter, drill, tap, turning insert, boring bar, turning tool holder etc. It refers to any piece of equipment which is used to modify the workpiece.
- Ensure the correct tool/insert is being used. If you are unsure, please contact our sales or technical team who will be happy to advise.
- Tool pull-out lengths should be at a minimum for maximum rigidity.
- When milling, always aim to use high performance chucks (e.g. Hydraulic Chuck, Shrink Fit Chuck, Power E-Hydro Chuck) as they create a vibration-reducing dampening effect, which will be far superior to using a standard collet holder or side lock grip.
- Using multiple helix geometry end mills (e.g. V7 Plus, X-Speed Rougher, TItanox Power) offer higher feed rates, larger depth of cuts and help eliminate vibration due to the special flute technology which breaks the cuttings off and interrupts the harmonics.


Program refers to the computations made to determine the path, speed, feed, timings etc. of the tool, so can play a part in creating chatter in machining.
- Ensuring the correct feeds and speeds are used alongside the correct depth of cut are crucial.
- The direction the tool paths are programmed. Tool engagement will determine the surface finish. If the end mill is cutting with 20% of the tools diameter and comes to a corner and a change in direction, for a split second the tool engagement may be 40% and you will hear that chatter before you see it! Programming the job so the tool path is at a constant engagement will overcome any chatter problems.
If you are struggling with chatter or vibration in your set-up, just give our Technical Team a call who will be able to walk you through the steps you need to take to eliminate or reduce this.
We also offer on-site visits where our Technical Application Engineers will be able to help optimise your tooling setup and suggest cost-saving, productivity-increasing solutions.
Call 01924 869615 or email sales@cutwel.net today!